2-XYZ-Phi System with nanometer stability for microassembly and miniaturization
Handling and Production
782477:001.26
Positioning holding accuracy in a nanometer range
This highly stable assembly system for high-precision lasers consists of an 8-axis positioning system and a substructure designed for ISO 5 cleanroom conditions and UV compatibility. It has two independently operating processing heads (Y1, Y2, Z1, Z2, Phi1, Phi2) on a common X-axis. The Phi axes are mounted on the Z axis. This allows 2 components to be positioned exactly in space in relation to each other and held stable over a long period of time in a currentless, uncontrolled standstill.
This system was developed for the assembly of a laser for the Fraunhofer ILT. The institute has designed a laser for measuring the methane concentration in the atmosphere, which will be used in the German-French satellite Merlin in 2021/2022.
Specially developed for the assembly of miniaturized components
|
|
|
|
Special features:
|
Maximum accessibility for highly sensitive assemblies
This system is available for construction spaces of 600 x 400 x 200 mm³. The workspace in which positioning is to take place is defined as 430 x 220 x 100 mm³ and allows 180° swiveling without colliding with the positioning system (free travel).
The extreme stability is achieved by the combination of weight, use of air bearings and strong AC servos as well as ball screws. In addition to the solutions developed specifically for this special task, PMT160 precision linear stages were used for the Z axes and DT130 from our product portfolio for the rotary axes (Phi). All of the eight axes are driven and positioned by stepper motors. The positioning system complies with the required specifications and has passed all of the customer's acceptance tests with top marks.
Individual extensions and customizations
Engineering services include the fitting of the systems to your structure and the desired controlls. Furthermore, we develop prototypes and like to adapt the systems to the environmental requirements of your application particle emission, radiation, temperature, precision special parts manufacturing, working height, collision protection, safety concept, compensation factor and filter, sensor mounting, brake, decoupling, special lubrication, special colors, holders, adapters, special motors with pharmaceutical approval, comprehensive documentation, test protocoll, llife cycle tests
Application areas
Ideal for the production of more brilliant lasers, high-precision sensors and better imaging optics, laser microassembly, miniaturization of medical components and devices, aligning and soldering optical components in position, microassembly of pacemakers, cameras, insulin pumps, packaging semiconductors, innovative electronic packages, microprocessors, microchip
References
2020/10 Press Release Submicrometer Precision for Lasers in Space
782477:001.26 | X | Y | Z | Rz | |
[mm; deg] | 950 | 350 | 150 | n *x 360 | |
Position holding accuracy | [µm; deg] | ± 0.5 | ± 0.5 | ± 0.5 | ± 0.5 |
Positioning accuracy | [µm; deg] | 200 | 200 | 200 | |
[mm/s; deg/s] | 25 | 25 | 5 | 15 | |
Max. Load | [N] | 15 | |||
Motor |
| Stepper Motor | Stepper Motor | Stepper Motor | Stepper Motor |
Drive |
| Belt | Belt | Worm Gear | |
Feedback | Belt | Belt | Open Loop | Open Loop |
Used Standard Components
DT130-DC
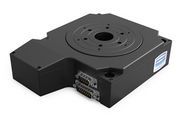
PMT160-DC
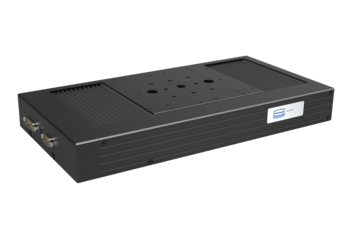
PMT160-EDLM
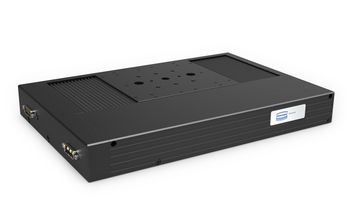
DT130-SM
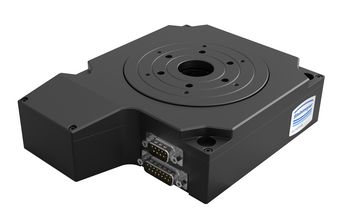
KGT 1214
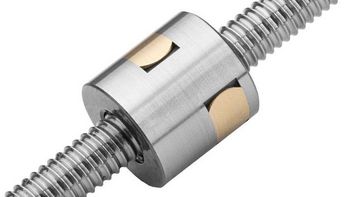
Are you looking for a technical solution for your application?
Get your first 3D Design in a few days:
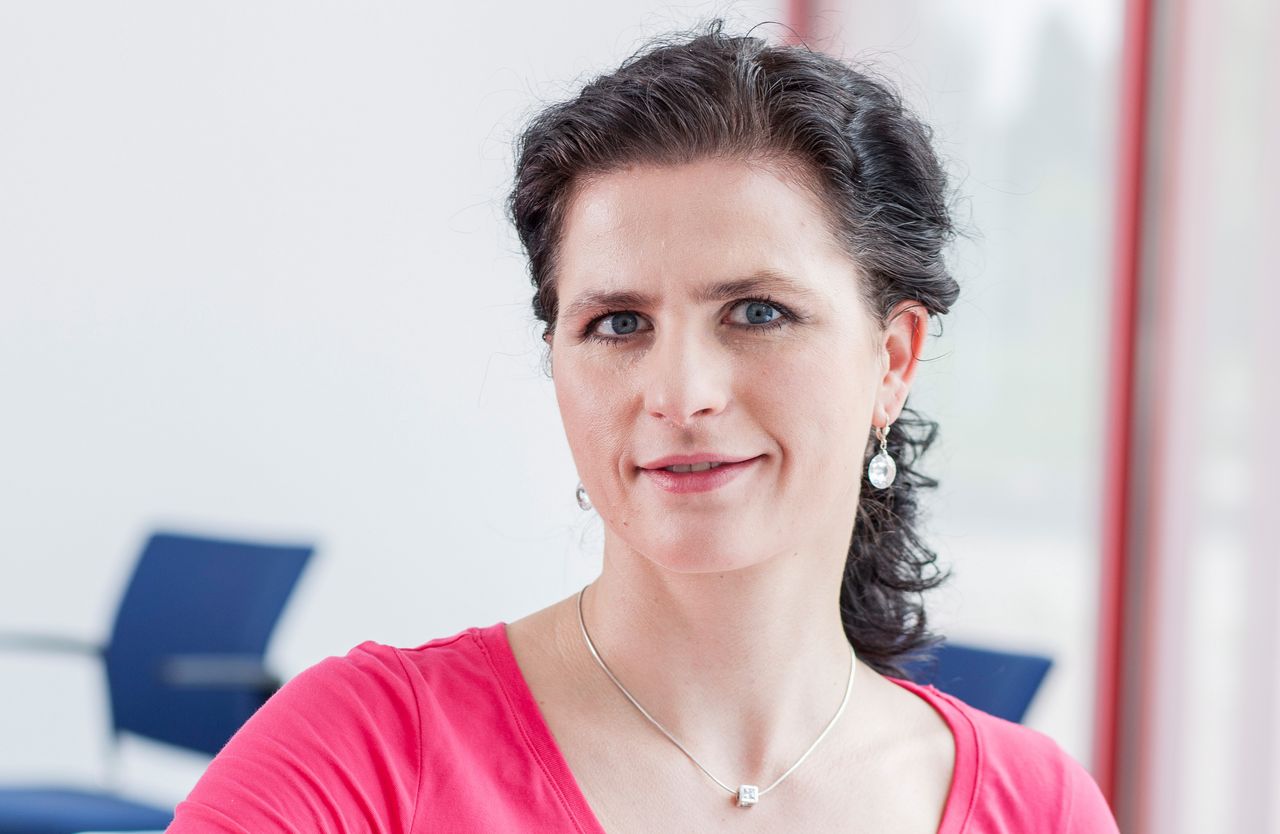
Katja Weißbach
Consulting
T +49 351 88585-64
E-Mail
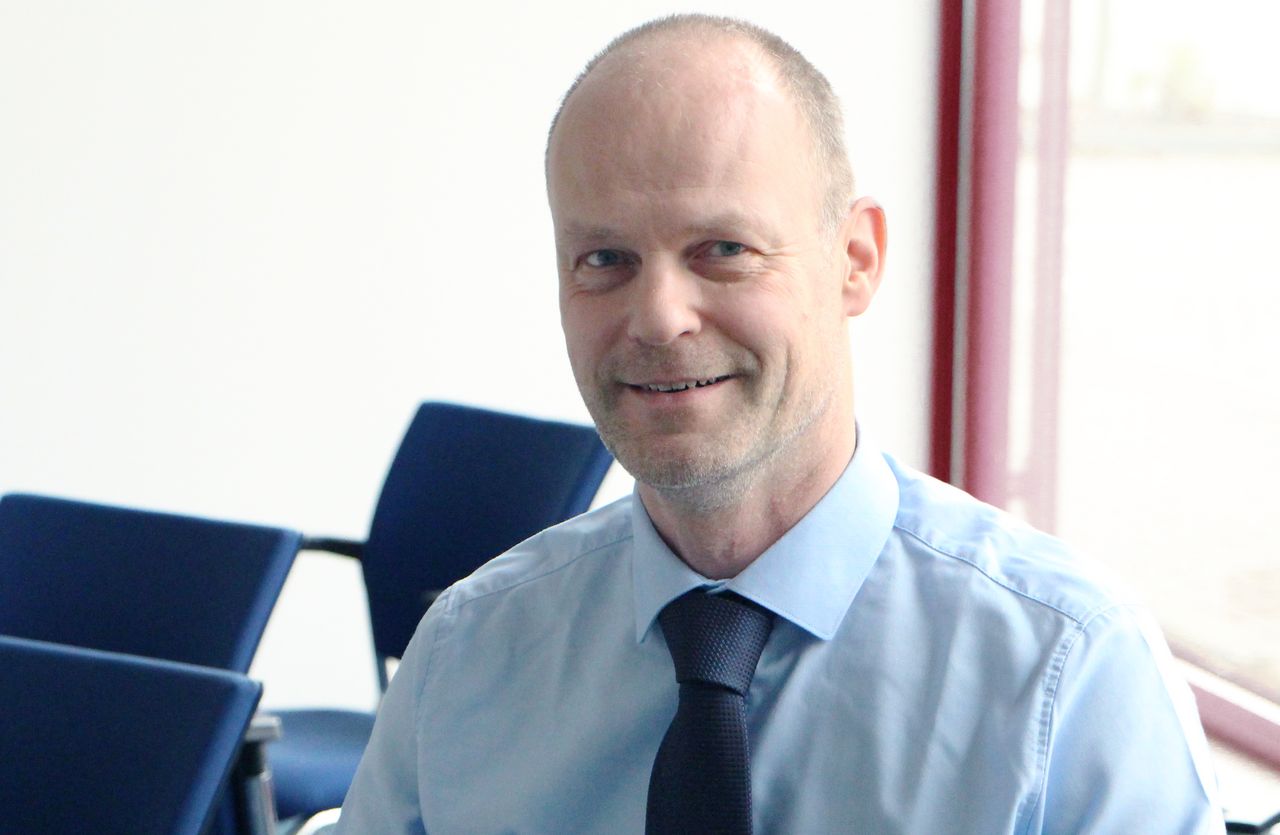
Ronald Schulze
Consulting, Project Management & Engineering
T +49 351 88585-67
E-Mail
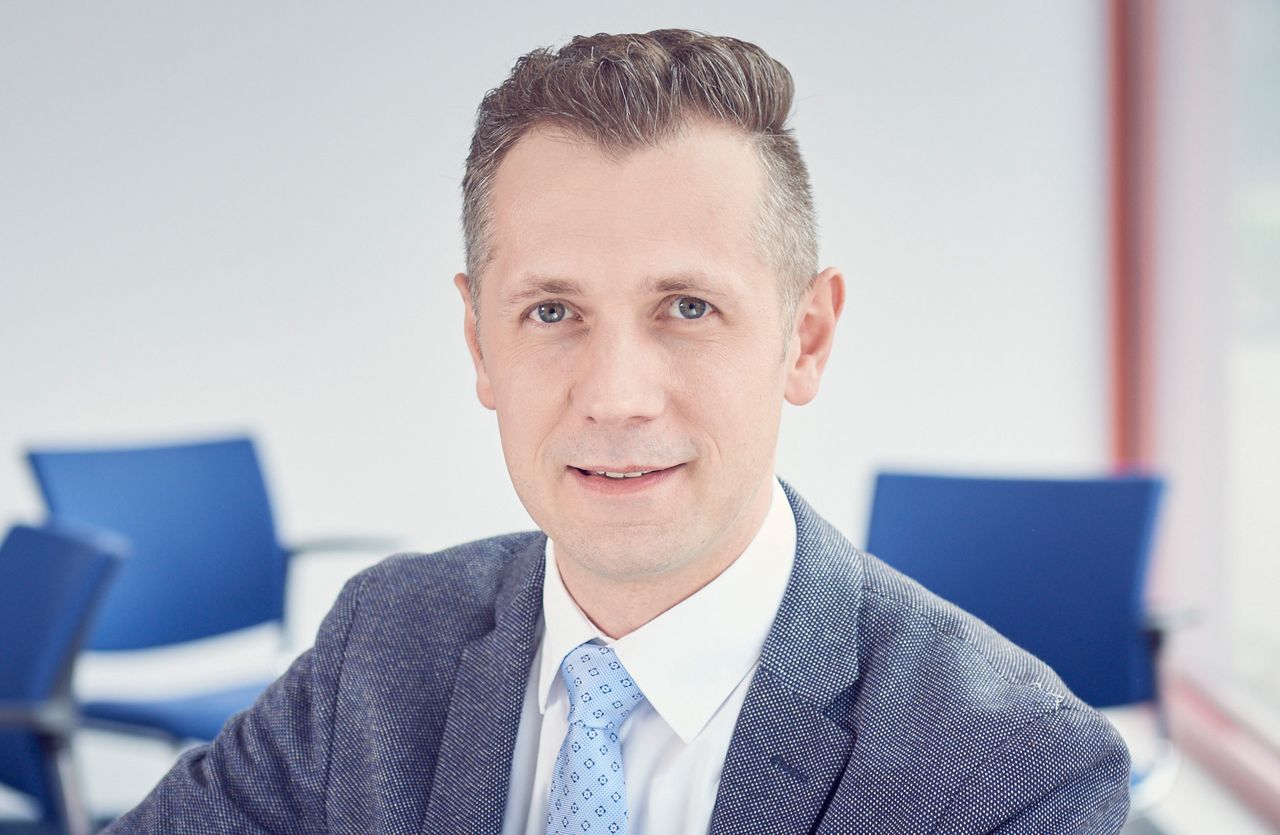
Francisco Samuel
Consulting &
Project Management
T +49 351 88585-85
E-Mail
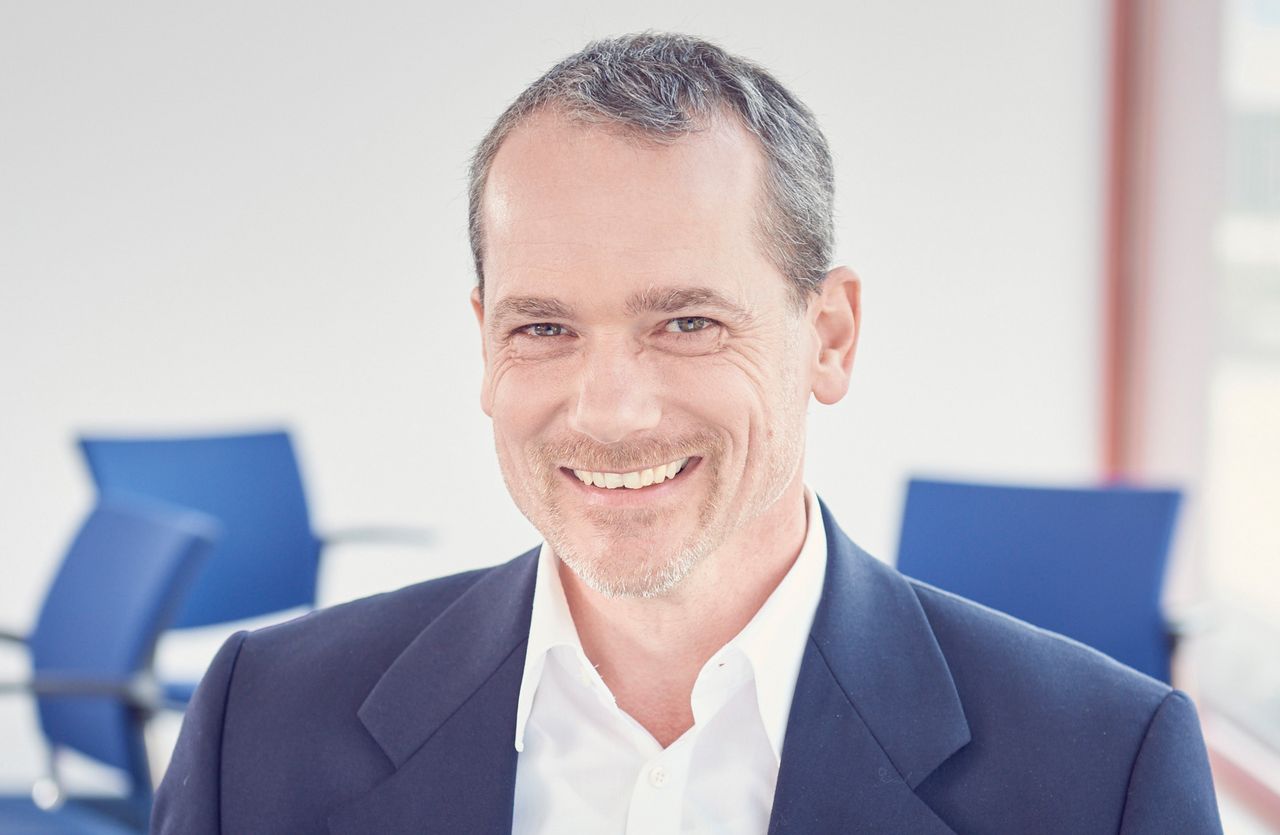
Elger Matthes
Consulting, Concepts, Innovation & Engineering
T +49 351 88585-82
E-Mail
Our references
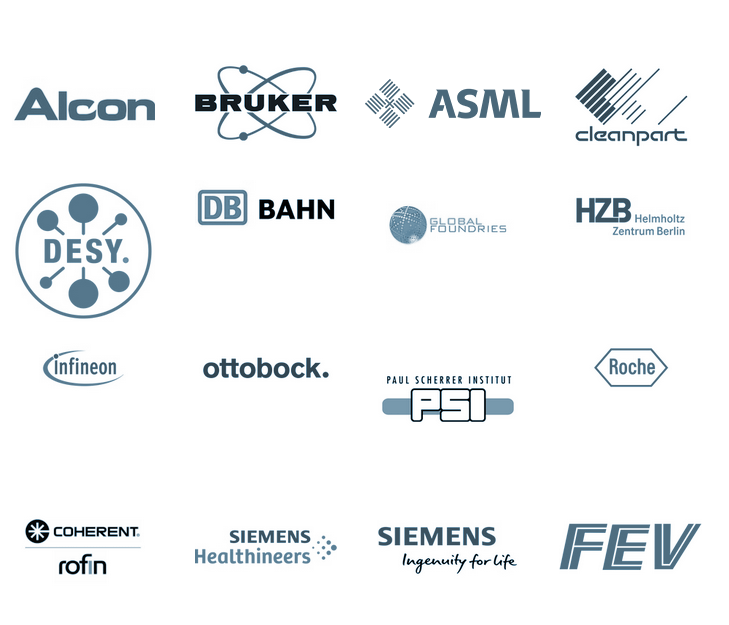